- 1. PROBLEM STATEMENT
- Goal Statement
Design Requirements
- Design Requirements
- Report Requirements
- 2. MANAGEMENT
- 2.1 Planning & Scheduling
- Planning involves identifying the key activities of the project (the tasks) and
ordering them into the proper sequence, while scheduling consists of putting the
plan into the required time frame. Your goal should be to scope the problem so
that you get an answer on time even though it may be necessary to sacrifice
accuracy and sophistication to meet the deadline. The schedule must be
continually updated and the scope and sophistication altered as necessary.
- Following the methodology recommended here and in the following sections,
ensures an early solution (approximate), and whatever time remains can be used
to improve the accuracy.
- Bear in mind that the design of a complex system is a multi-disciplinary,
multi-task effort where one task depends upon the successful completion of
other tasks. A proper schedule will include man-power requirements and
allow them to be leveled over time so that there is no idle time. There
are many scheduling methods available, ranging from simple bar charts to
computer-based scheduling systems such as CPM (critical path method) and
PERT (program evaluation and review technique). The planning and scheduling
of the preliminary design activity, is of course only a part of the planning
devoted to the total design/manufacturing.
- 3. SOLUTION
3.1 Approach
- Planning
- This constitutes the plan we use to solve the design problem.
Ullman
suggests 4 different kinds of plans:
- fixed plan: fully specified steps, or "cookbook" approach
- list of plans: select one from a list of solution approaches taken from previous
experience
- parameterized plan: a set of steps is prescribed along with the design parameters
- search: a search is made through a number of design solutions.
The search method is most appropriate for our purposes. It means we will select
feasible solutions satisfyng all criteria from a set of syntheses.
Key parts of the approach plan include:
- Clear understanding of the problem statement
- Specifying the criteria
- What basic physical principles are involved?
- Word description of steps to be taken
- Lay out tasks involved
- Gathering information
- Scheduling
- Scheduling of efforts within tasks and to meet the
final presentation objective are much the same as
discussed under Management above.
-
3.2 Modeling
- Physical Model
- Design Criteria
The design criterion functions are the objectives in functional form
(dependent variables);
They are the state variables used to make the evaluation of
the criterion specified for solution, while satisfying the design requirements
In some cases the criterion function may be obvious, perhaps the total manufactured cost
or the life cycle cost of an item; but in other cases it can be difficult to define.
In fact it is sometimes necessary to include more than one criterion.
A single composite objective may then be taken as a weighted average
of 2 or more individualcriteria.
Let us suppose there are n such objective functions
and we can write the composite criterion :
The scaling factor is required to make all contribution have the same,
or at least consistent, units (we must be careful not to compare apples with oranges).
Where possible it is probably better to use a single criterion.
Then, if time and need exist, a second one might be assessed to aid in making
trade-offs. The importance of choosing and justifying an appropriate objective
or composite objective though, cannot be over-stressed.
- Mathematical Model
Functional Constraints
- Use simplest equation/tabular relations which will give
sufficiently accurate answers to establish feasibility
- Refine these equations to give the necessary accuracy
when proceeding to the Evaluation step
- List those functional constraints which give
the defining equations for the Design Criteria
(Do not list functions defining inequality constraint
variables here)
- List assumptions made and resulting limitations
Fixed Constraints
List fixed constraints
- fixed by nature
- fixed in problem statement
- fixed by designer
Design Parameters
List the design variables.
(These are the state variables which are to be varied to
satisfy the Criterion Functions)
- For the first time through:
- Give a "best guess" value to all state variables
- Use values from a pre-existing, well-understood solution
wherever possible
i.e. Build upon what you know already.
Justify values given
- Perform degrees of freedom budget if appropriate
Inequality Constraints
- Develop & list functional expressions for the constrained
(inequality) variables
- Design requirements are specified by federal &state
regulations, the conceptual designer, the customer,
the designer
3.3 Nominal Solution
- Analysis
- The initial goal is to obtain a single feasible solution for each concept
and then
be in a position to understand the problem and the importance of each of
the design parameters (some were previously estimated).
(May be able to use simple calculator-based estimates
for this purpose and improve the accuracy at a later iteration)
- Develop a solution algorithm for the Criteria Functions
using
the constraint sets developed above
- Note: some of the equations may be transcendental and require
using an iterative
root-solving routine.
- Develop algorithms for determining inequality constraint functions
- If you are certain your solution must lie on an inequality line, you
may find it convenient to change it to a functional constraint.
This too, is often transcendental in nature and requires iteration
using a root solver.
- Obtain a solution
- Feasibility Assessment
- Change design parameters until
feasible results (all constraints satisfied) are obtained
- If a physical feasible result cannot be achieved for any concept
make certain you understand why, and can defend your conclusion
- Re-assess the problem statement particularly with regard to the
fixed constraints imposed.
- If these cannot be altered, discard the non-feasible concepts.
3.4 Evaluation & Decision
- Design Space Studies
This first of all, is a time to study the scope of the problem, and
to obtain an understanding of the design space.
Specifically, it is a time to:
- establish the number of design parameters of importance
- make a count of the number of functional constraints (equations) required
to define the criterion function and
the number of fixed constraints, thereby determining the potential
number of degrees of freedom in the design
- select and justify candidate design parameters
- make an estimate of the total range we need to consider in each of the
design parameters
A good understanding of the design space can now be best obtained by varying the design
variables and observing the resulting criterion function and inequality constraints.
If the design variables are chosen in pairs, graphical display offers the best way
of observing and assessing the results. Carpet and/or contour plot and/or
surface plot programs then use the data base to give
a display of the design space.
A look at all candidate design variables now allows us to consider the importance of each
of them, and to judge whether we can make some of them fixed, but only if we can conclude
that they have little effect on the criterion function within the design space prescribed.
This should allow us to begin to reduce what is potentially an excessively large problem
at this stage. There will be design parameters whose importance you are not sure of at
this point. To get a measure of relative importance of each candidate design variable,
we can perform a sensitivity analysis at various locations in the design space.
Let us define the criterion function F as
- n is then also the number of degrees of freedom
Then the sensitivity of the objective function to any design variable can be defined
as 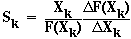
Using the nominal solution algorithm to evaluate F at closely spaced values
of a design parameter
then will give us the sensitivity of F to changes in that parameter. In fact, the carpet
plot data base can be used to obtain the sensitivities.
- There are some dangers in applying this approach to determining which
variables result in the highest sensitivity since, if the nominal solution happens
to be near an optimum solution then S ~ 0. It is necessary to determine S at several
widely dispersed points in the feasible design space therefore.
Comparison of the sensitivities of each design variable will then allow a
determination of which design variables may be given a fixed value, and
thereby reduce the number of degrees of freedom of the problem.
- The carpet/contour plot of course gives us an excellent indication of where
these sensitivities should be determined. In fact if the design parameters are all
chosen to be non-dimensional the slope of lines on the carpet plot can be used as
direct indications of relative sensitivities of the parameters.
- Iteration
Here we begin to march toward a solution which satisfies the criterion. We will assume
that this involves a means-end process like an optimization process and we are
attempting to minimze a criterion function.
If the preceding steps have been followed properly,
then the problem is well-posed and there is a unique,
best solution which of course satisfies the inequality constraints.
Since in general, some of our equations in engineering design are in tabular
and graphical form it is not possible to use some of the mathematical tools,
such as Lagrange multipliers, to search for optima. Instead we use numerical-based
approaches. There are two general approaches commonly used:
- A Graphical Data Base Search
- A graphical display of the design space allows us not only to find the optimum,
but also to "see" the solution behavior near the optimum. The disadvantage lies primarily
in calculating and storing the huge data bases required, and in our inability
to display graphical solutions where there are many degrees of freedom to the
problem; it is difficult to plot a surface in multi-dimensional space.
In any event, the graphical display should always be used to follow the solution,
making sure that it is behaving properly prior to attempting a direct numerical
optimization.
It is sometimes possible to reduce the effective number of degrees of freedom by using
optimal relations for a few of the design parameters within the algorithm.
- A Numerical Search
- The inequality constraints are translated into equations or are treated as boundaries,
and a search is made for the appropriate extreme in the criterion function;
most available software requires that the criterion function be written in such a fashion
that a minimum is to be obtained. There are computer programs available using
a variety of approaches, beyond our scope here, which search for the optimum.
The disadvantage of this approach is that the end result is a "number";
no indication is given to us of the properties of the solution, such as how
broad is the optimum, how sensitive is the answer to a relaxing of inequality
constraints unless they are treated as parametric constraints. This is overcome
by altering the constraint line and assessing the sensitivity of the
criterion function to that change, or by the use of combined graphical/search
methods.
- The approach to be used is obviously dependent upon the problem complexity.
For our purposes we will limit ourselves to the graphical approach for small
problems since it is normal to have a graphical display in a workstation
environment for fast interaction between designer and computer.
For large problems, (those with many degrees of freedom) we will use numerical
search techniques after an initial graphical study.
- 4. PRESENTATION